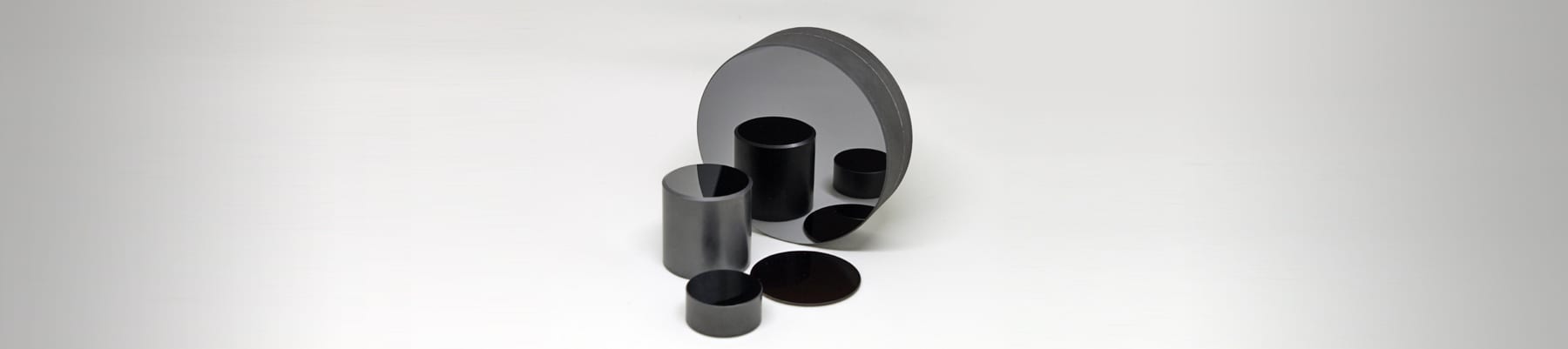
Lapping & Polishing
Achieving Smoother Surfaces on Ceramic and Other Hard Materials
Lapping is the process of using a loose abrasive between two surfaces that rub together, thus abrading the part. Typically, lapping is used to achieve a surface roughness and flatness beyond the capabilities of standard grinding.
Deciding the combination of abrasive and lap material to use is a choice that’s based on the type of material being lapped. That decision is critical because the choices will affect material removal rates, surface roughness, and the lap’s ability to hold its form.
A softer lap allows more of the abrasive to embed in it and produces a better finish with less material removal. A harder lap enables the abrasive to roll “freely” and produce more removal. The tradeoff, however, is that the finish will not be as good as one performed with a softer lap. Along with the changing of laps, abrasive size decreases accordingly to yield better finishes.
Polishing is similar to lapping in concept, but the process of removing microscopic surface roughness (asperities) is complicated. Polishing can involve the removal of molecule clusters at an atomic level. It occurs at such a small scale, which often makes it difficult to explain effective ways to remove asperities.
There are differing opinions on how, and why, polishing works, with a majority of what we know coming from empirical data.
Depending upon the component material and kind of abrasive used, mechanical and chemical removal mechanisms can work together or independently to achieve the desired result. Another polishing consideration is the kind of material used as the lap. A lap can range in hardness from cast iron or tin to wax or pitch.
Tell us about your application.
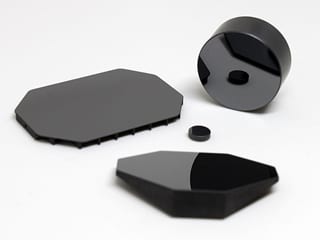